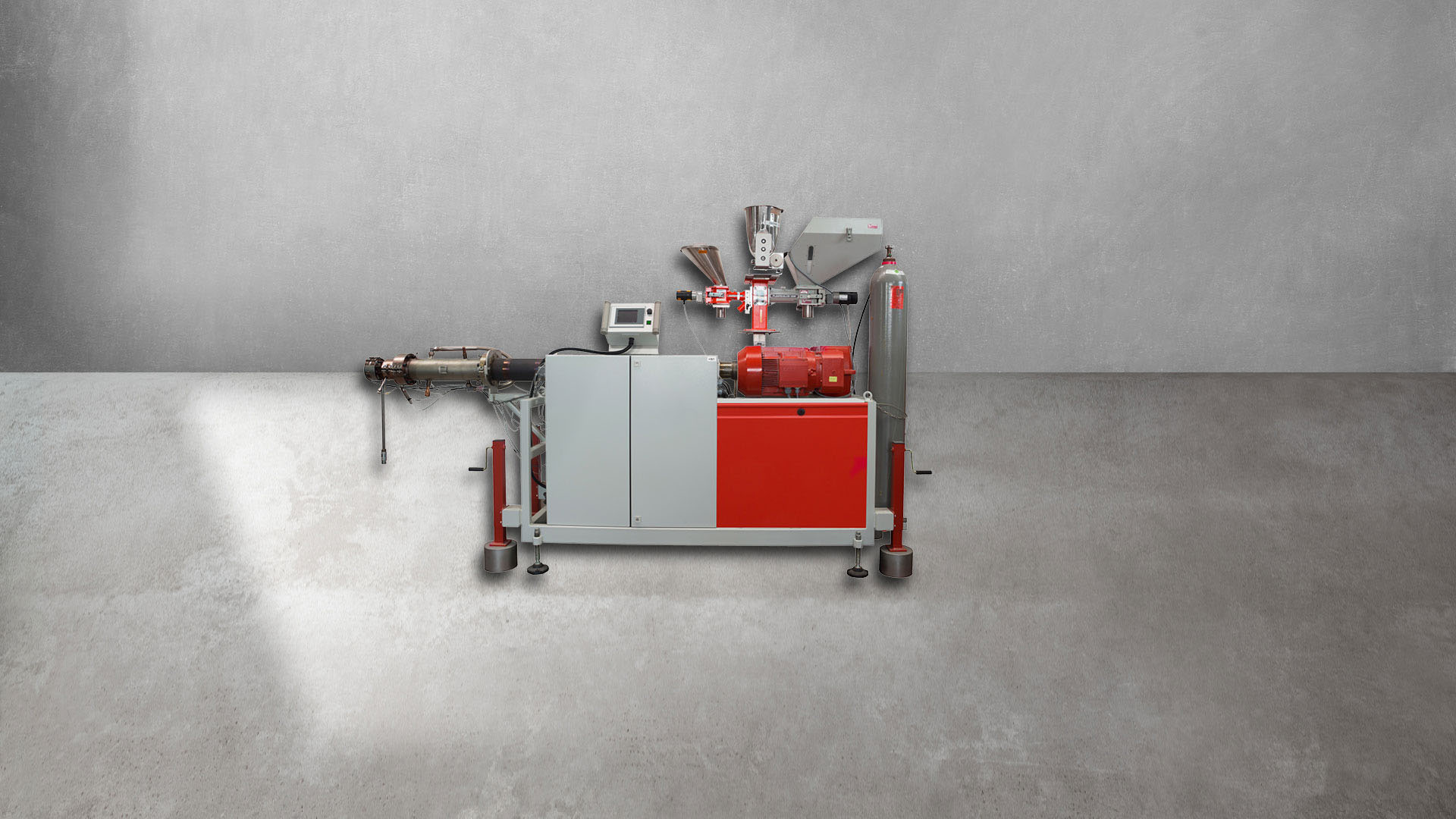
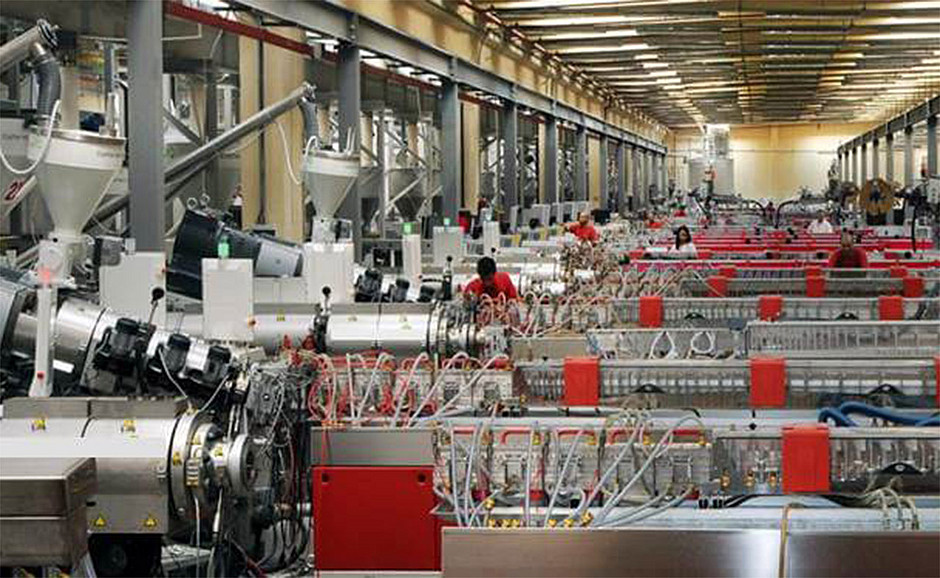
Twin-screw extruders
For any performance areas.
Exelliq offers twin-screw extruders for any scope of application.
In addition to the output and the individual application, many other process parameters are perfectly balanced so that your desired result can be achieved. The Exelliq tuning experts are at your side with their extensive and deep understanding of materials.
We closely cooperate with the top extruder suppliers in the industry. All our tuning experts are very familiar with all types of extruders.
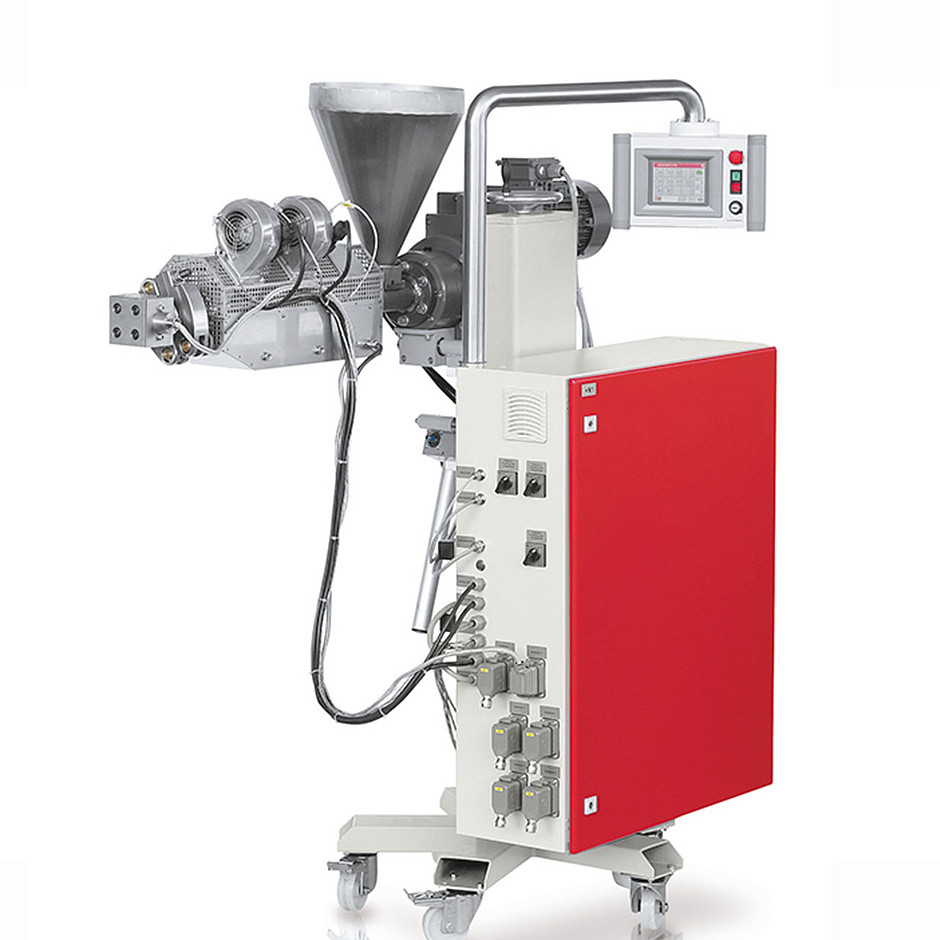
Single-screw extruders
Vast process experience.
Single-screw extruders by Exelliq are used for smaller output ranges. The variety of processing materials is almost limitless. Trust in our extensive process experience for your successful production.
In the extrusion process, the end product also determines the requirements of the extruder technology. The single-screw extruders by Exelliq are used worldwide as main or co-extruders and, precisely set, fulfil the defined customer requirements. Single-screw extruders made by Exelliq are the perfect solution not only for technical profiles but also for small profiles for windows and doors.
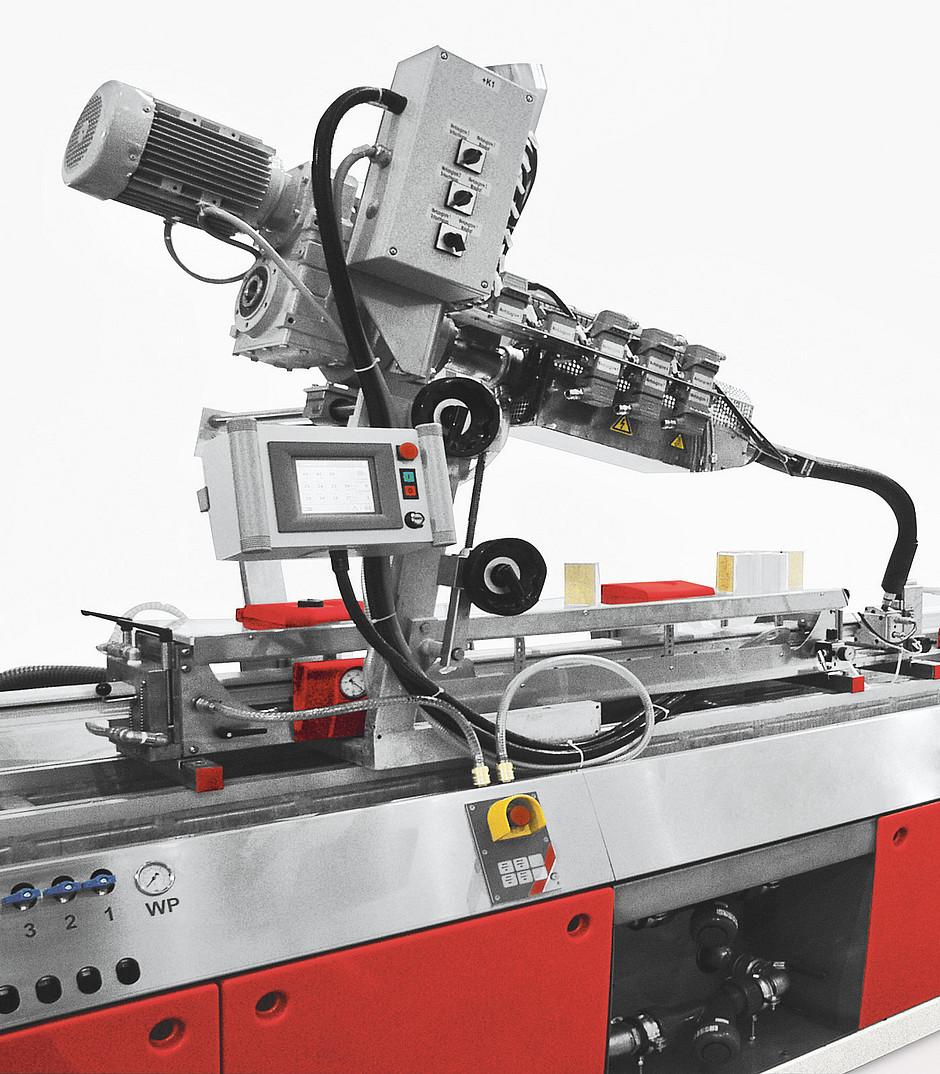
Co-extruders & PCE extruders
Perfect adhesion of your gaskets.
The Exelliq co-extruders are used for extrusion into or onto gaskets made of PVC-p, TPE or other extrudable elastomers – both during the co-extrusion operation and the post co-extrusion operation. Furthermore, it is possible to weld rigid PVC profiles to rigid PVC is possible (grooved locking). We offer 2 different types:
- GCE type F: directly mounted to the calibration table and is thus a space-saving solution to produce gaskets.
- GCE type T: is mounted on a chassis.
It is operated using an operating panel via touch screen. Faults and alarm messages are displayed for early troubleshooting. In addition, the control offers a general overview of the current production status and shows the target vs. actual values of the last 40 production minutes. You can save tooling-specific settings to speed up the next start-up process with the same tooling.
Heat current monitoring of all heating zones enables early detection of a heater band break, resulting in scrap reduction. The standard equipment also includes two cylinder cooling zones.
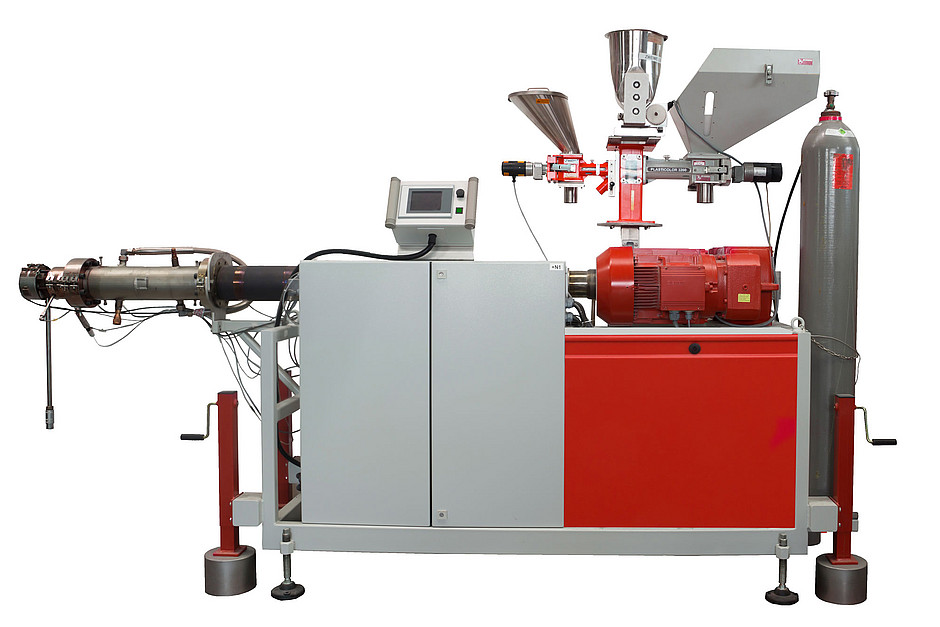
FOAM.EX
The foam extruder for optimal material combination.
The foam extruder made by Exelliq was developed for WPC profiles with an in-line foamed core. The technology perfectly combines the advantages of a full profile with the benefits of a hollow chamber in the end product.
Advantages of WPC profiles with physically foamed core compared to WPC full decking profile:
- Up to 50% in input material savings through weight reduction
- Up to 46% in material cost savings
- Up to 32% reduction in production costs
- Improved dimensional tolerance