RED.TOOLING – the premium profile tooling
Excellent profile quality. Low operating costs.
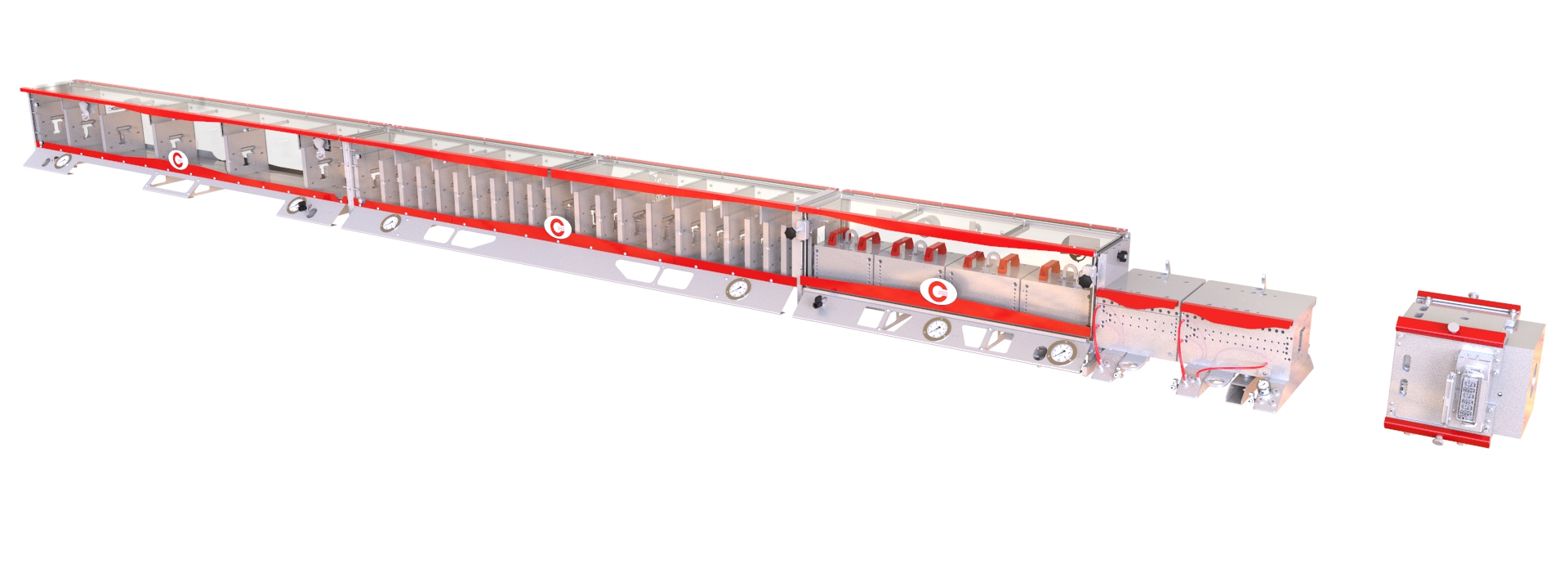
Ahead through superior profile quality and low operating costs.
RED.TOOLING meets the highest requirements in profile extrusion and is setting new standards with its unique features such as a heater cage with a central plug, PDC technology, roller short calibration or options like FLOW.CONTROL, FLOW.MATIC, air support control,roller tuner, and the KEEP.CLEAN unit.
- Superior surface quality
- More material savings
- Higher energy and water savings
- Increased productivity
- Longer service life
- Total process reliability
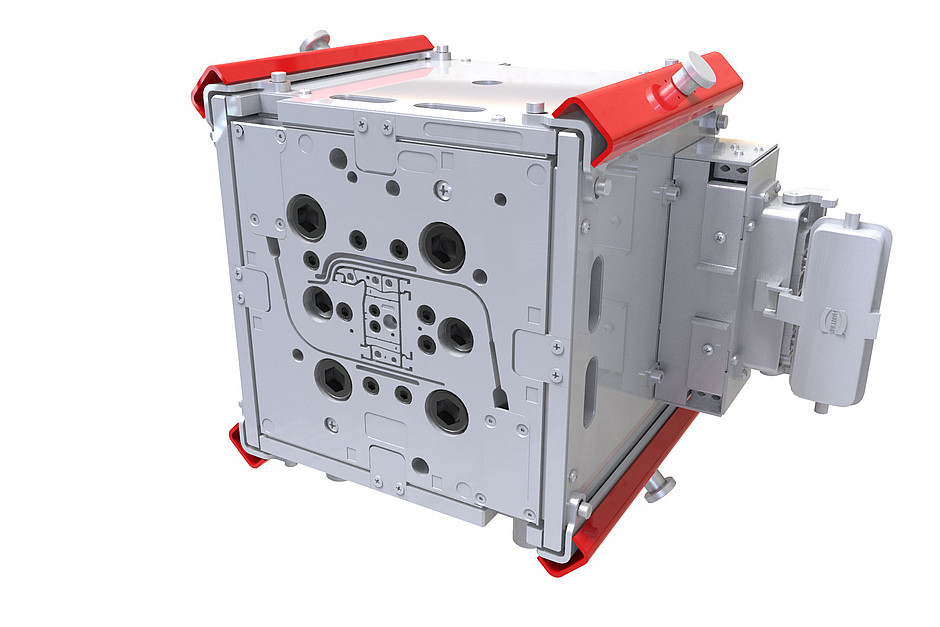
Heater cage with central plug
Only one central plug-in connection between the die and the plastic extruder rules out a mix-up. The new heater cage boosts safety and increases productivity.
- Design extremely clear: 1 plug-in connection, 4 fixing screws
- Reduction in scraps because no risk of mixing up the connection
- Safety system (double-wound) with visual monitoring
- Simple and quick assembly and disassembly
- Integrated temperature sensor rules out cables from breaking
- Standardised dimensions of the heater cage
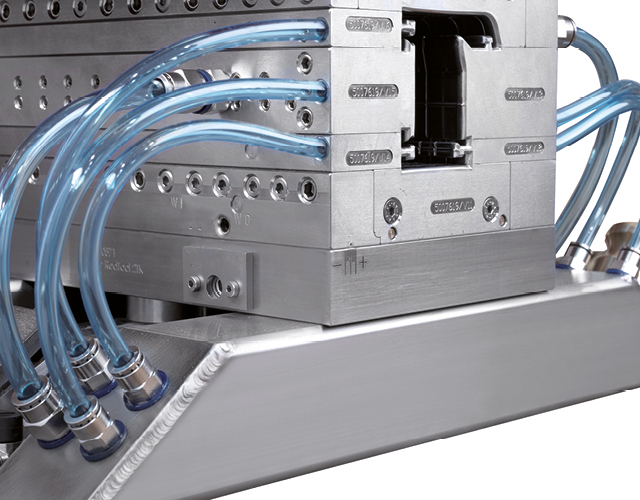
RED.TOOLING dry calibration
The RED.TOOLING dry calibration stands out with its extremely efficient use of the valuable resources water and energy. At the same time, it shines with an increased cooling capacity.
- Safety feature to keep lid from slamming shut
- Centralised media supply
- A patented block seal prevents unregulated air entry
- Together with GESS, 80% of all geometries can be produced with only one vacuum pump and one cyclone unit
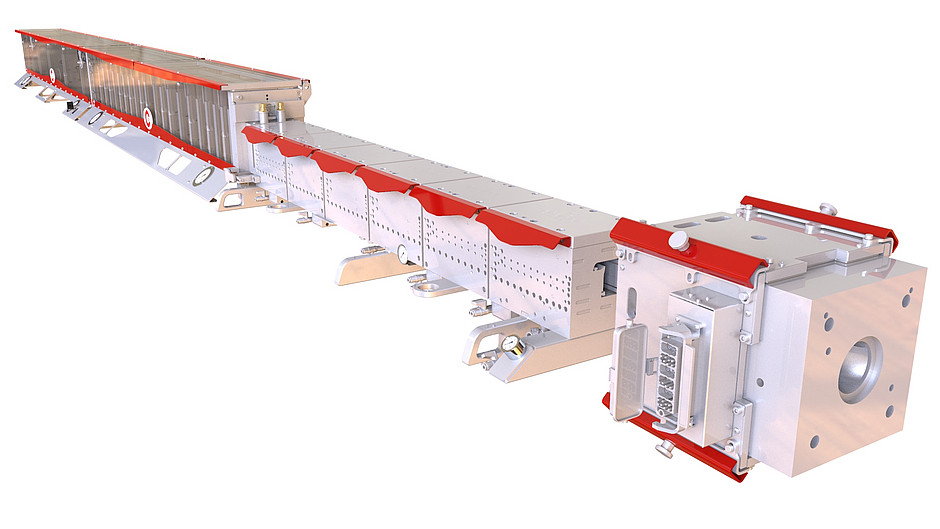
RTx.0 dry calibration
Especially for high-plate-out mixtures, the premium profile tooling RED.TOOLING is available in the RTx.0 style and does not require PDC technology. The RTx.0 dry calibration is particularly resistant to hard deposits inside the calibration and also comes in a tubeless version.
- Ideal solution for high-plate-out formulations
- Little to no line adjustment necessary
- Tubeless option – even inside the hinged lids
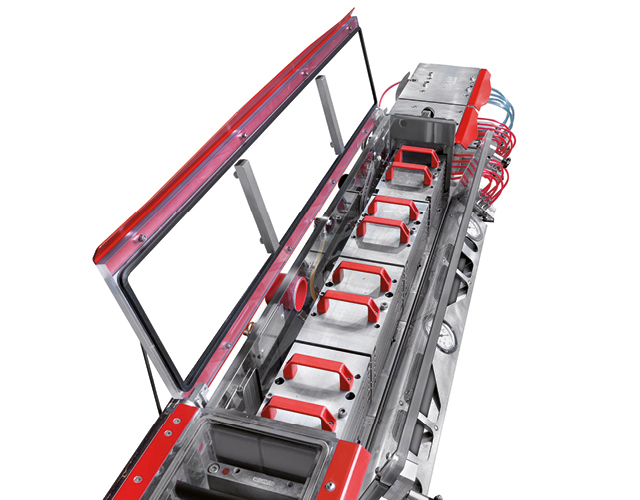
RED.TOOLING PDC tank
Direct cooling in the PDC tank improves process reliability and minimises quality fluctuations. The intelligent use of direct water also reduces energy consumption.
- Maximum output
- Geometry of the profile remains stable
- Easy, quick retrofitting and cleaning
- Better profile shrinkage values due to direct cooling
- Significantly fewer sources of error – no connections/sealing rings/special cooling systems
- Shortened preparation time for coating
- More than 35% can be saved in water
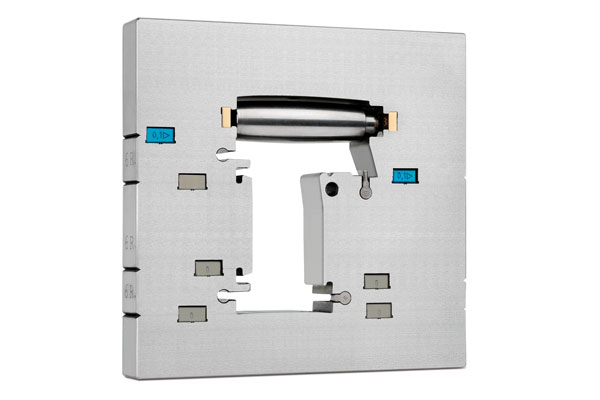
RED.TOOLING roller short calibrations
The roller short calibrations improve the surface quality. They reduce scratches from appearing on the profile by up to 80%. No EDM wire cutting for re-working needed, which allows for faster reaction times and shorter downtimes. In addition, the roller short calibrations are compatible with the DIGI.TANKsystem when performing an upgrade.
- Scrap reduction due to score-free profile surface
- No EDM wire cutting for re-working needed
- Fast reaction times and short downtimes
- Position control with colour coding
Savings: c. €5,500 p.a.
Window frame example: 1.2 kg/m, 5,000 h/a production time, 1.2 €/kg material costs, 350 kg/h output
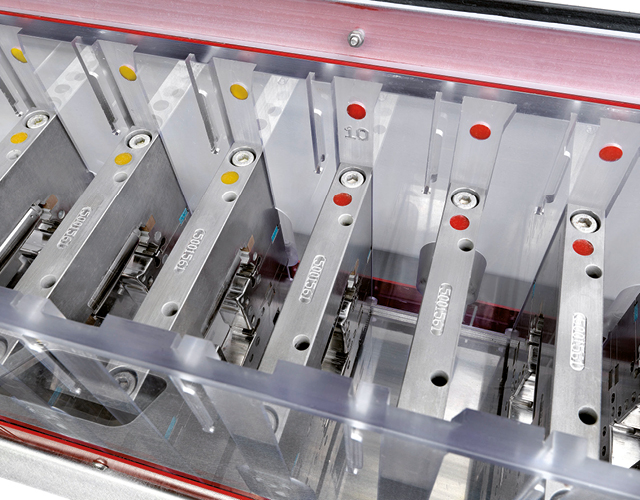
RED.TOOLING vacuum tank
The vacuum tank operates quietly and combines high transparency with the utmost break resistance. It reduces water consumption by up to 50% and, in combination with GESS, significantly reduces energy costs. Furthermore, the RED.TOOLING tank can be upgraded to the DIGI.TANK system.
- High transparency enables process control
- Increased tightness reduces energy consumption
- Vacuum manometer placed in the steel substructure in a shatterproof way
- Lighter, dimensionally stable and divided lids
- Self-regulating water level
- Coupling system accessible from the operator side
- No makeshift solution for drying due to drying chamber in the last tank
- Increased work safety due to muffled closing mechanism
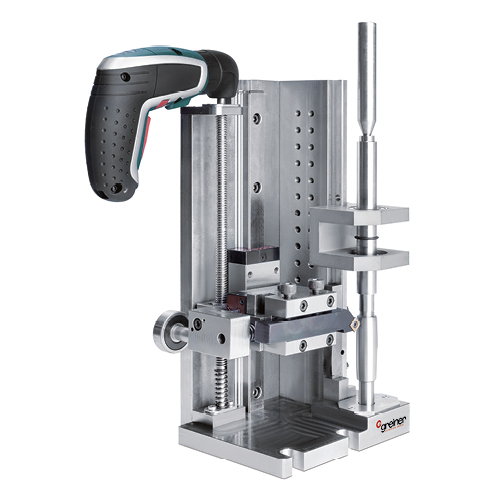
Roller-changing device
Roller-changing device to easily re-work rollers on conventional milling machines.